TECHNICAL REQUIREMENT
Deburring and trimming: Remove excess metal
- Origin: Burrs present after plasma cutting and torch cutting.
- Objective: Improve surface quality.
Descaling: Remove scale
- Origin: Residual scale present during the steel manufacturing process.
- Objective: Improve welding conditions (clean surface, less smoke generated) Improve paint adhesion
Improve welding quality by avoiding the creation of undercuts (At the time of welding, fusion of the adherent scale and cracking at the part).
Deoxidation: Remove the oxide layer on the edges
- Origin: Oxidation of the edge during CO2 laser cutting (bluish contour).
- Objective: Improve the adhesion of the paint on the edges and avoid corrosion.
Edge rounding: Round off the part's sharp edges
- Origin: Sheetmetal cutting, stamping, machining.
- Objective: Secure part handling operations.
Degreasing: Clean the part and remove any grease
- Origin: Oiled sheetmetal, cutting oil, machining oil.
- Objective: Improve the next operation in the production flow (welding, painting)
Surface preparation: Give the part sufficient roughness
- Origin: Smooth blanks
- Objective: Allow for good adhesion of paint or galvanisation
SOCIO-ECONOMIC NEEDS
Whether it is an approach dealing with automation, the replacement of an unsuitable or over-consuming resource, the need revolves around the following three points:
Productivity
Deburring and descaling of plasma or torch-cut parts is a tedious and costly process. Even if automation is not essential, unlike other means of production such as cutting or machining, it's a significant source of savings.
Profitability
The purchase of a means of production is calculated on the basis of the investment but also on the daily operating costs. The question of operating cost is paramount when it comes to investing in a finishing means. The use of the deburring tumbler represents a low operating cost. The installation is reliable and robust with low consumption in terms of energy, spare parts and abrasives. The return on investment is therefore rapid, usually in less than a year.
Improvement of working conditions
Improving working conditions may be the primary reason for investing in a semi-automated or automated finishing solution such as the deburring tumbler. Following a work accident, such as cut when using the grinder or when the Committee for Hygiene, Safety and Working Conditions (CHSW) requests developments towards more EHS-friendly devices, SPALECK INDUSTRIES is able to provide an appropriate response.
YOUR PROCESS
There exists a variety of machining/cutting technologies and they are constantly evolving. We strive to provide finishing solutions that are adapted to the following processes:
- Precision machining
- Laser CO2 cutting
- Plasma cutting
- Torch cutting
- Fibre laser cutting
- Stamping
- Additive Manufacturing (AM)
- Press cutting
YOUR APPLICATION
The applications are many and varied. SPALECK INDUSTRIES strives to find a solution for all types of applications. This list is not exhaustive.
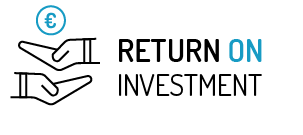
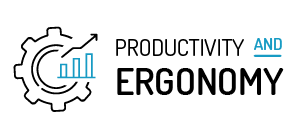
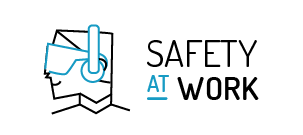